The MiTek Modular Initiative, which has backing from Warren Buffett’s conglomerate, is betting big on modular construction—something few companies have been able to navigate successfully.
For decades, architects and businesspeople have argued that the construction industry is ripe for industrialization. Taking the messy, slow, and costly process of building away from the job site and into a streamlined factory has been a dream for everyone from iconic architects and designers like Frank Lloyd Wright and Buckminster Fuller to present-day companies like Assembly and Bone Structure.
Now, a new venture from a company inside Warren Buffett’s Berkshire Hathaway conglomerate is taking on the challenge of creating and scaling modular architecture. With the big-budget backing of a parent company that’s worth hundreds of billions of dollars, the initiative may just have a chance to succeed at creating cheaper and faster buildings where so many others have fallen short.
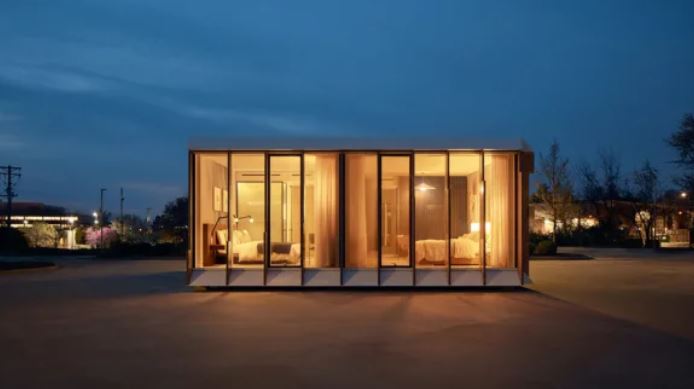
There are plenty of hurdles to making this type of construction process work, from the high overhead of building and running factories to the regulatory and labor challenges of getting unconventional construction approved. Then there is the issue of making sweeping changes in the construction industry itself, a large, decentralized, and risk-averse business. Few companies have been able to both turn the ship and navigate these complicated waters.
The folks behind Berkshire Hathaway’s project hope their experience will be different. Formally launching today, the initiative is a joint venture between MiTek, a construction software and building services company, and New York City-based Danny Forster & Architecture, which has designed several high-profile modular buildings, including one that will soon be the tallest modular hotel in the United States. Their approach combines Forster’s firsthand knowledge of the shortcomings of modular construction and the wide range of construction companies under MiTek’s umbrella, including a manufacturer of structural steel, a maker of high-rise building facades, and a maker of the fireproof wall boards that line the insides of buildings around the world.
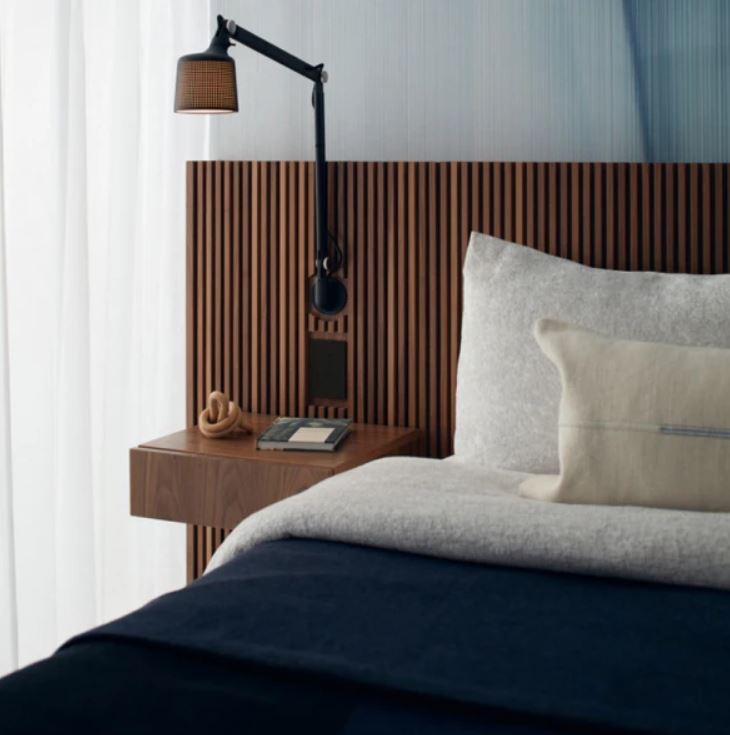
Forster’s firm joined with MiTek about a year ago to establish the MiTek Modular Initiative, a long-term investment in developing a new approach to factory-based modular construction that has an undisclosed amount of backing from Berkshire Hathaway. The company says the investment numbers in the millions of dollars. Through an innovative approach to making the modular steel boxes that form the literal building blocks of this type of construction and optimizing how and where they are outfitted with utilities, interiors, and facades, the Modular Initiative could overcome the challenges that have held other efforts back.
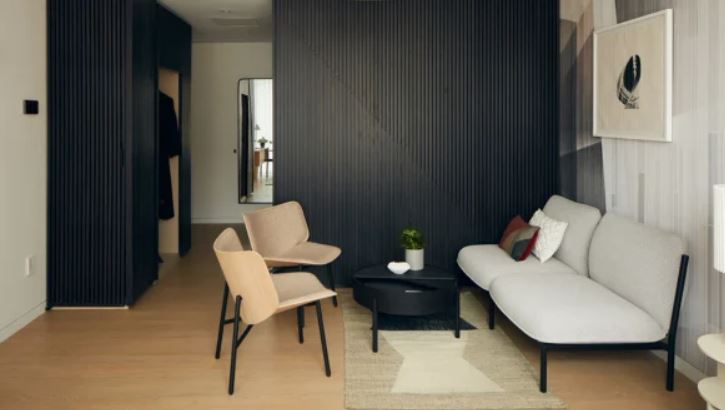
Constructing buildings in a factory is not new, and MiTek’s Modular Initiative is certainly not the first to try to make industrialized construction work at a bigger scale. Companies like Houston-based Katerra and Sekisui Heim, the homebuilding arm of Japanese conglomerate Sekisui Chemical, have managed to survive as vertically integrated builders, while many smaller prefab companies have either folded or been subsumed by others.
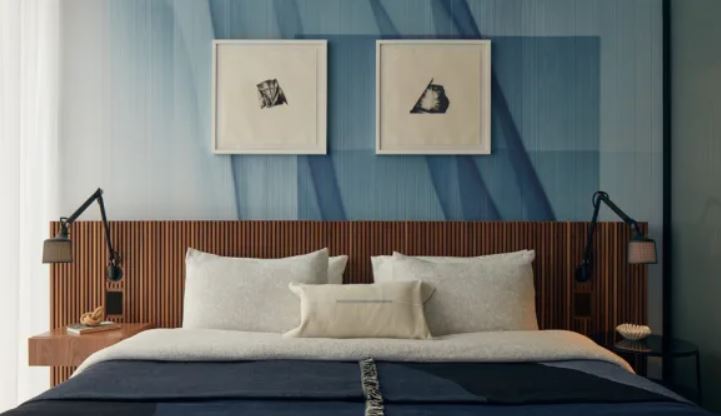
MiTek’s innovation is a module that can fold. Instead of large steel boxes that have to be carefully routed under bridges and overpasses on the back of a truck, MiTek’s collapsible modules fold flat, easing transportation to job sites. That broadens the geography the company can reach, compared to the roughly 400-mile radius a typical modular builder can service economically. Without factories sprinkled across the country, most modular builders can scale only so high. MiTek’s approach would send its preconstructed flat-pack modules to be finished and assembled wherever the project happens to be. “This is one major step towards decentralizing the supply chain and saying modular can happen all over the country, because you’re not schlepping these massive things,” Forster says.
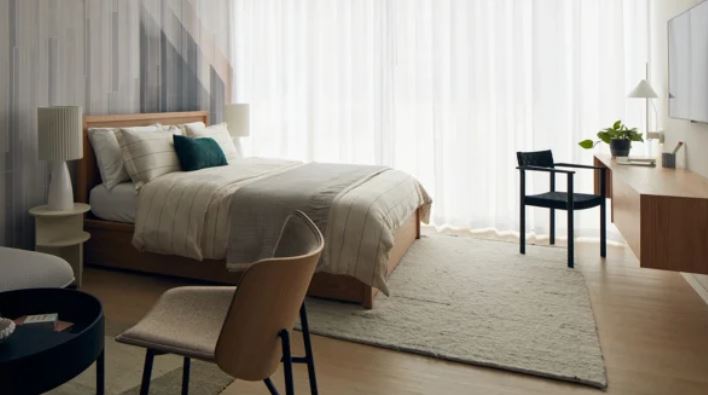
These pop-up plants, as the company calls them, can be created as needed in already existing warehouse spaces near building sites, using equipment rented from MiTek to outfit each module like the last stages of an assembly line. That means most of the actual building of a modular project can happen locally, and by local labor—a key selling point for labor unions and the city officials who control the approvals of major projects.
Labor unions have not been entirely welcoming of these kinds of factory-based projects, which can bring down the total amount of labor hired to do construction work. A 2019 report on modular construction from McKinsey found that shifting to off-site construction would cut labor costs by about 25% compared to conventionally built projects. Though some of this labor shifts into the factory, the total amount of labor used tends to go down.
These are complicated dynamics that Forster knows well. His firm is currently working on a modular tower in downtown San Francisco, where obtaining city approvals for the unconventional project has required an added level of negotiation. “The unions have told us very clearly there’s no way in hell you’re shipping in a building from offshore or even from out of state. They’ve said if it’s not 40 miles from the job site and local labor’s not participating, it’s not happening in downtown San Francisco,” Forster says. The project is in the process of receiving local approvals. It could eventually be built using MiTek’s process.
The actual construction of modules has been one of the major choke points for big modular projects in the U.S., according to MiTek’s Ullom, who says there just aren’t enough factories and companies capable of building them at prices that can compete with factories in places with lower labor costs. “To date, most of the high-rise modular buildings that have been built in the U.S. are built using offshore labor,” he says. According to a recent report on the anticipated growth of the modular construction market, most factories are located outside of the United States.
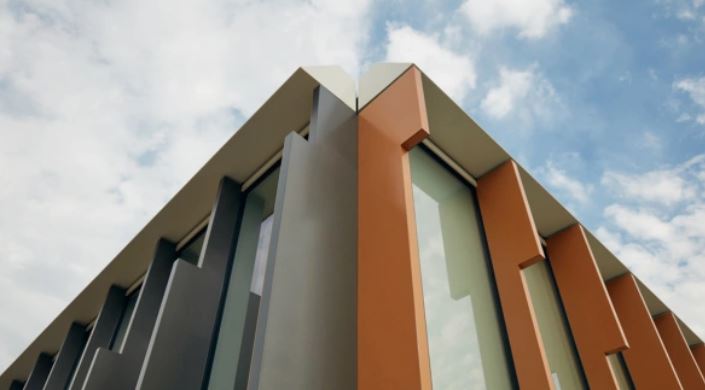
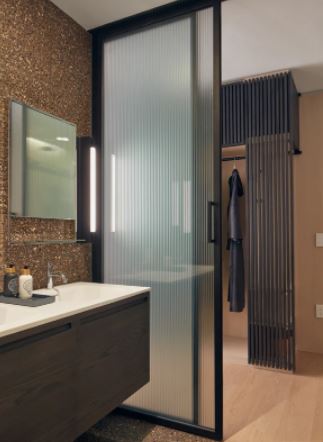
Striking a balance between improving the efficiency of construction and maintaining jobs will be a challenge. Ullom says the company has been in talks with about six large general contractors. But as a former general contractor himself, he knows they’ll take some convincing. “It’s a big leap to go from the way we build today to, ‘Oh, we’re going to go do this in a plant,’” he says.
One of the ways MiTek may get general contractors on board is by finishing as much of the module as possible in its own factory, sending the flat-packed boxes to pop-up plants with labeled boxes of precut parts that construction workers would simply need to put together—more Ikea than Lego. Ullom says the company will be spending the rest of the year refining its processes, and plans to build more prototypes in the fall. He hopes MiTek will begin module production early next year.
But neither MiTek nor Berkshire Hathaway is in any rush to go to market. Forster says they’re approaching this as a long-term investment in determining precisely how to disrupt the construction industry. “This probably comes from Mr. Buffett,” Forster says. “Not a lot of companies can say I’m taking a 10-year look at this.”
Even with that time and the luxury of Berkshire Hathaway’s deep pockets, a lot about the construction industry would have to change for something like this to succeed, from the work practices of general contractors to local permitting rules to building inspections inside manufacturing and assembly facilities. MiTek wouldn’t release the names, but it claims to be in high-level talks with two major national builders about implementing its approach on future projects. If that were to happen, and if the company is able to get its module-based approach off the ground, construction could become faster and cheaper. For now, these are big ifs. History suggests they won’t be overcome easily.